Maintenance can be defined as the orderly control of activities required to keep a facility in an as-built condition, with the ability to maintain its original productive capacity. Maintenance management simply involves controlling maintenance activities.
A good maintenance management system makes equipment and facilities available. Availability means the production team can demand and receive any item, such as light, power, air, gas, heating, cooling, or machine tools, when it is needed. If the required equipment or service is down, or if the machine stops short of completing a job, time and money are wasted. A good maintenance management system helps accomplish minimal downtime.
The fundamental steps of maintenance management are simple and beneficial to pursue. The basic steps of maintenance management are request, approval, plan, schedule, performing work, recording data, accounting for costs, developing management information, updating equipment history, and providing management control reports. The following is a brief review of the events that occur during each of these steps. Also see below:
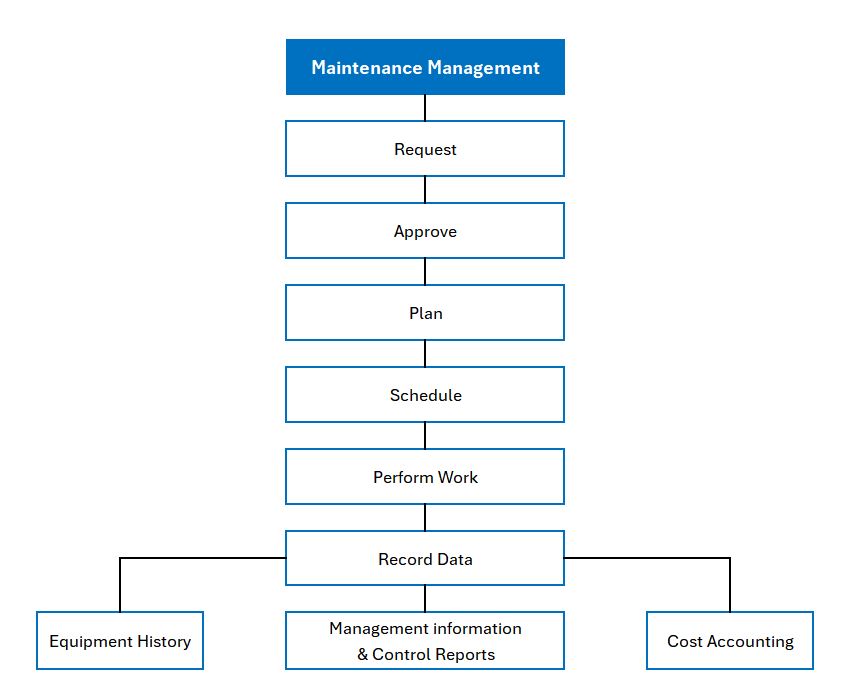
Fundamentals of maintenance management.
- Request. Requests to perform maintenance work may be transmitted in different ways- verbal, written, electronic, and the like.
- Approval. Maintenance supervisors often handle simple jobs (small expenditures); however, large expenditures require approvals from several levels of management.
- Plan. Ensure resources are available (material, labor, tools, equipment, and so forth). The planning step can take many forms. For example, the maintenance supervisor can give verbal orders to the crafts. people, and if a planner is used, he/she will prepare a work order.
- Schedule. Scheduling involves three factors:
- Priorities. Priority codes are based on established criteria or on the importance of the equipment and the type of work.
- Job assignment. Jobs are assigned to maintenance technicians.
- Follow-up. Follow up to make sure the job is being done.
- Performing work. The work is performed based on information received by craftspeople. Sometimes they receive little or no instructions, and sometimes they are provided with detailed procedures.
- Record data. The data recording may vary from a simple listing of the actual hours to keeping comprehensive records of material charges, equipment identification, work assigned and performed, and other pertinent data.
- Accounting for costs. It is important to know where your money is used and what you purchase with the money.
- Developing management information. This may involve providing facts on current work, including costs, accumulated data, equipment identification, productivity, budgets, and scheduling.
- Updating equipment history. History records might include little or no data, or might show updates of all equipment, records, equipment use, downtime, maintenance labor, and material costs.
- Management control reports. As management information is developed, control reports covering expenditures, performance, backlog, and equipment data, for example, are generated regularly to summarize the results of the maintenance function. These reports are very important for plant managers to make appropriate and intelligent decisions.
Overview of CMMS
Computerized Maintenance Management System (CMMS)
A computerized maintenance management system (CMMS) is a computer software program designed to assist in the planning, management, and administrative functions required for effective maintenance.
These functions include the generation, planning, and reporting of work orders (WOs); the development of a traceable history; and the recording of parts transactions.
CMMS is not just a means of controlling maintenance. It is now used as a means to ensure the high quality of both equipment condition and output.
CMMS offers core maintenance functionalities. It is not limited to manufacturing; it is applicable to facilities, utilities, fleet, and other types of organizations where equipment/assets are subject to wear, and repairs are done to them.
A CMMS usually includes equipment management, preventive maintenance (PM), labor tracking, WO, planning, scheduling, inventory control, and purchasing.
CMMS usually does not include financial or human resource management (other than basic cost recording and personnel information). You can, however, integrate them with financial and human resource applications.
Enterprise asset management (EAM) evolved from CMMS. With EAM, the CMMS functionality is extended to include financial modules such as accounts payable, advanced cost recording, and advanced human resource management.
CMMS Modules:
A basic CMMS includes:
A. Equipment data management
B. Preventive Maintenance
C. Work Order Management
D. Labor
E. Scheduling/Planning
F. Vendor
G. Inventory Control
H. Purchasing
I. Budgeting