This module is used to define all pieces of equipment/asset, spare parts, run time, and safety procedures, and to set up schedules for PM. You can add new pieces of equipment to the database, define relationships among equipment, enter and track equipment locations.
You can maintain complete maintenance history on equipment through WOs, which enables you to make decisions on replacing or repairing equipment. This kind of reporting can save time in analysis during an equipment life cycle.
Here we are focusing on the functional capabilities of the Asset Management module in the Evolve FM CMMS/CAFM software.
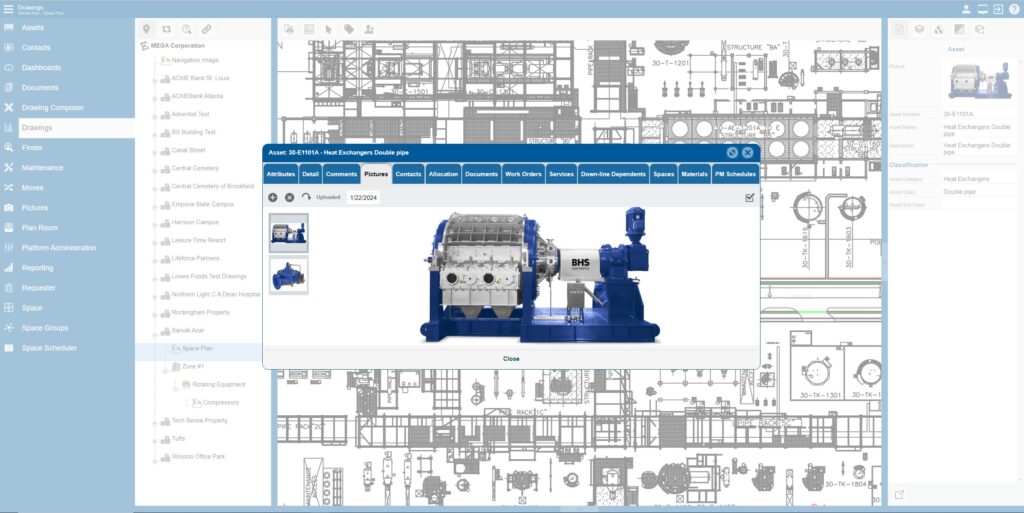
- Equipment hierarchies. Equipment can be identified and structured into parent/child hierarchies at higher level (cost center, maintainable unit, and department) or at lower level (component, subcomponent, or spare part). Defines equipment classes and assigns each equipment to a class to include function, location, vendor, or criticality.
- Equipment identification. Provides equipment master descriptive information for a piece of equipment (parent/child), manufacturer, serial number, spare parts/bill of materials listing, equipment specs, repairs performed, failure causes, costs, and so forth. May include the capability to record the installation and removal of components within process type operations that require tracking by serial number and compliance to process safety management requirements. Performs full-text searches using keywords in the description.
- Equipment inquiry. Online top-down view of equipment structure with a minimum of five levels and online view of equipment com-ponents/parts. May include graphical capabilities to show site layout with drill down to department/work center, specific asset, and sub-components included as part of the equipment parent/child rela-tionship.
- Regulatory and special requirements. Provides data supporting the definition and maintenance of equipment and component regulatory information, permit requirements, and special requirements such as fire protection.
- Equipment spares inquiry. Obtain spare parts/bill of material list from equipment master data that are component parts of an equipment asset. Add, change, or delete items from spares list or copy spares list to another asset. Also, copies all or part of spares list to a work-order job plan and creates parts requisition and pick list to storeroom.
- Equipment spares update. Adds, changes, or deletes equipment spares information via mass updating capability.
- Parts interchangeability inquiry. Obtains a list of all the equipment assets that use a stock item based upon MRO information. Provides cross-reference link to specifications data for the MRO item.
- Warranty information. Tracks warranties on newly installed or repaired equipment/components and provides information to maintenance when a work order is created for item still under warranty. Enters warranty and shelf-life information into the system when item is actually received.
- Equipment maintenance history. Provides complete repair history for equipment/components with online access.
- Equipment failure information. Tracks failure information at various levels: equipment, component, subcomponent, or spare part. Provides for recording of failure cause and corrective actions taken.
- Equipment parent/child relation. Attaches/detaches/reassigns equipment parent/child hierarchies. Adds, changes, deletes, or reactivates equipment asset information and asset specifications.
- Equipment operations data. Provides for equipment usage or measurement data being entered directly or tied to process control or equipment monitoring systems as means to trigger actions such as inspections. Data on operating factors and their high and low trigger points, which indicate abnormal operating conditions are established and maintained.
- Equipment service. Provides data on operational status, outage schedules and out-of-service history based upon downtime captured from work order or manually entered. Data may be used to support “availability element” calculation for establishing the overall equipment effectiveness (OEE) factor.
- Equipment inquiry by parent. Obtains all subsidiary (“child”) equipment information for a specified equipment “parent.”
- Equipment cost history inquiry. Obtains equipment historical actual costs for equipment “parent or child” or rolled-up costs for an equipment hierarchy. Updates historical maintenance costs for a piece of equipment (parent/child) via work-order closing.
- Equipment support documentation. Information in the equipment master data that provides reference to drawings, specifications, calibrations data, technical reference manuals, performance standaras, and other asset support documentation that needs to be viewed or printed for repair or troubleshooting activities related to the equipment. Direct links to document management systems (DMS), computer-aided drafting/design systems (CAD), regulatory compiance data, and other systems to support asset documentation may be established.
- Location history. Supports the entry and review of location and installation history data for serial numbered items and regulated components that must be specifically tracked.