Functionality-The Important
Evolve FM CMMS Features
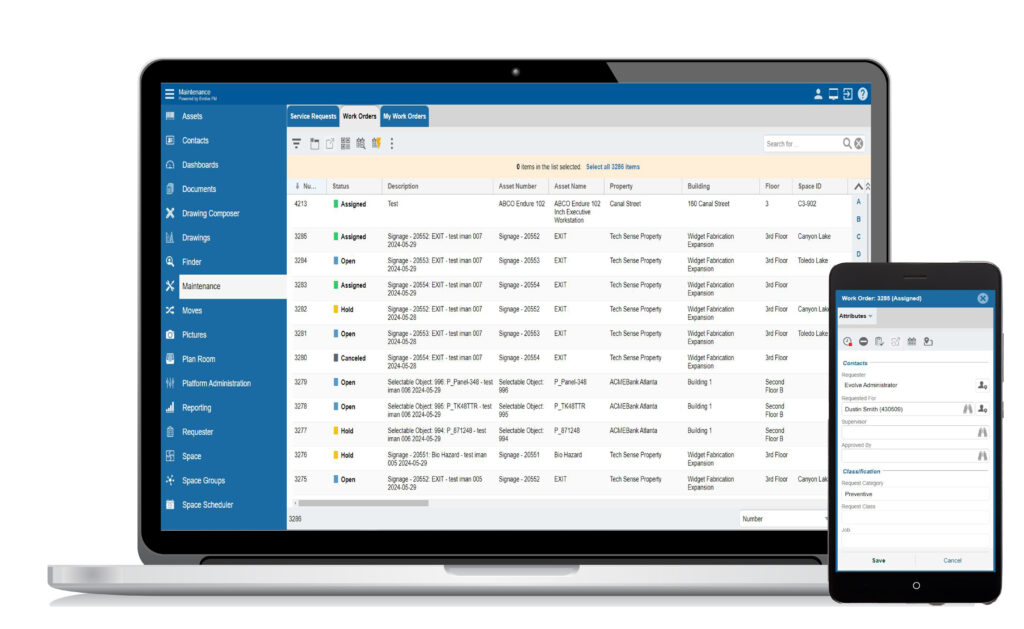
The functionality capabilities of a computerized maintenance management system (CMMS) are the features that provide the benefits of information technology for maintenance operations. Effective CMMS enhances and is an important enabler for almost all best practices. The important first step is deciding, “Where you are” with today’s best practices and current CMMS functionality. Next to “define where you want to go” a plan of action for best practices such as an effective storeroom, formal planning and scheduling, more effective preventive maintenance (PM), and predictive maintenance (PdM) is developed. A new or upgraded CMMS may in fact be a major part of the plan. Now we can define the functional requirements needed for a new CMMS or gaps within an existing CMMS. This is also about benchmarking your functionality needs versus what the CMMS vendors say they can provide to meet your needs.
This post will help to define CMMS functional requirements so that an evaluation and selection process can address specific needs and then support the right choice for your specific maintenance operation. We will present extensive definitions of CMMS functional capabilities and provide a convenient rating method to use for making a detailed comparison of CMMS functional capabilities of multiple vendors.
Making the Right CMMS Choice
Before progressing to the evaluation and selection phase of CMMS, we must understand our specific needs. It is important to benchmark and formally evaluate current practices of your maintenance operation. This identifies best practices that are needed. A strong commitment to implementing best practices brings with it the need for effective information technology in the form of CMMS. To make the right CMMS choice and gain maximum value from our investment we must define CMMS functional requirements. Most CMMS systems include the basic functional capabilities associated with the core modules for:
c. Inventory management/maintenance repair operations (MRO) materials management
e. Preventive maintenance and predictive maintenance
f. Purchasing g. Other CMMS functional capabilities
Advanced levels of functional capabilities may include the need for purchasing capabilities or greater capabilities for budget and cost control, project management, or being able to use CMIMS with links prints, assembly drawings, parts catalogs, or other documents. The following CMMS functional capabilities are defined according to the CMMS module where they are typically included. We will cover the functional capabilities of the core modules first and then cover advanced functional capabilities.